Richard Lange, F. A. Lange’s first-born son, can take credit for numerous inventions and patents that had a decisive impact on the evolution of precision horology. His most important discovery is still relied on today in nearly all high-quality mechanical watches: the admixture of beryllium in balance-spring alloys. In 1930, Richard Lange was granted a patent for this invention, which redefined the benchmark in timepiece precision.
The balance spring, or hairspring, is the heart of a mechanical watch and as such directly responsible for its rate accuracy. Depending on the spring type, a thickness deviation of merely 0.001 millimetres will cause the watch to be off by about 30 minutes per day. Accordingly, the manufacturing tolerance is an incredible 0.00005 millimetres. The production of balance springs is one of the most complicated processes in precision watchmaking. Only a handful of watchmaking companies master the operations, among them the Lange manufacture, where particularly high quality standards are attained. At A. Lange & Söhne, a special mathematical formula is used to determine the optimal hairspring for each individual calibre.
Review: the balance spring production – A. Lange & Söhne
MATHEMATICAL PRECISION – GUIDED BY HAND
Process step 1:
At the beginning of the manufacturing process, the spring wire has a diameter of 0.5 millimetres. During the first step, it is drawn through diamond dies of varying sizes.
Depending on the watch model for which the hairspring is intended, the wire is drawn as many as 32 times. After the drawing sequence, the diameter of the wire for the RICHARD LANGE PERPETUAL CALENDAR “Terraluna”, for example, is a mere 0.059 millimetres.
Rolling
Process step 2:
Now, the extremely thin wire is rolled flat to its final dimensions. After the rough and finish rolling passes, the wire has a thickness of 0.022 to 0.044 millimetres and a width of 0.08 to 0.17 millimetres, depending on the model.
At Lange, the tolerance is one ten-thousandth of a millimetre, a hundredth of the diameter of a human hair. In these minuscule dimensions, quality controls based on laser measurements are no longer sufficient. To verify compliance, it is also necessary to weigh a defined length of the strip with a precision balance.
Cutting and coiling
Process step 3:
In this step, the strip is first cut to the proper length and then coiled into its typical spiral shape. To achieve the exact spiral geometry, three to five strips are coiled together, again depending on the model. After annealing, the strips are separated from one another. Now, they have the precisely defined coil clearances they need to “breathe” (oscillate).
Annealing
Process step 4:
At this point, the tightly coiled strips are heated for 12 hours with controlled temperature cycling and then cautiously allowed to cool again. This causes them to retain their shape and gives them the required resilience.
The temperature cycle is permanently monitored, recorded and evaluated by instrumentation, because even the slightest deviations or disruptions would suffice to render the hairsprings unusable.
Bending
Process step 5:
At A. Lange & Söhne, the bend points of each hairspring are accurately determined according to a special algorithm. Under the microscope, the hairspring is secured to a template, allowing its end to be carefully bent with specially designed pliers. Bending requires extreme dexterity and rigour; only the most experienced hairspring truers are capable of mastering this challenging task.
Pairing
Process step 6:
The last step involves matching the hairspring to the balance-wheel rim. To ensure the utmost in precision, a matching hairspring is selected for each and every rim. A highly sensitive frequency analyser reveals which hairspring and which rim make up a perfect pair – and thus are fit to be integrated in a Lange watch.
Explore further



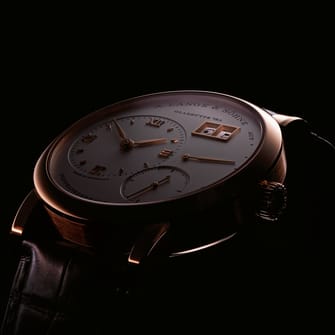
Exclusive insights into the world of fine watchmaking
Experience A. Lange & Söhne’s fascinating heritage, unique stories and exquisite timepieces by subscribing to our newsletter.
How can we be of service?
Whether you are in search of a specific model, have questions out of interest or need a service request for your timepiece – we are delighted to help you. We are at your service by phone, email or in one of our boutiques.
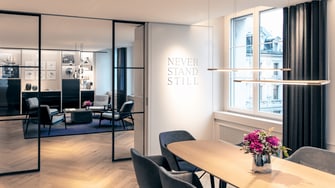