Watch connoisseurs can identify an A. Lange & Söhne movement at first sight. Each component is decorated with its own specific type of finissage, whether or not it is visible through the sapphire-crystal caseback. No matter how small it might be, each part must comply with rigorous artisanal and aesthetic standards.
It takes several months of practice just to perfectly execute a flat polished finish, while in chamfering, great emphasis is placed on assuring that the edges are not only bevelled to the same angle but also to the same width. A special type of finish is reserved for the balance cock: it is engraved with the Lange-style floral pattern that makes each Lange watch unique.
Immerse yourself in the intricacies of our artisanship with the following video clips. Discover what it takes in terms of effort and dedication to finish our movements.
The descriptions below of 11 Lange-typical finishing techniques provide fascinating insights into the work of our watchmakers and master finishers.
Every Lange timepiece, from the SAXONIA THIN, a simple two-hand watch, to great complications with a perpetual calendar or tourbillon are finished by hand.
Walter Lange on the finissage of a Lange movement
Finishing & engraving
Ribbing
The uniform stripes of the ribbing pattern decorate the three-quarter plate and the caseback sides of the bridges of a Lange calibre. They are produced by a slightly inclined, rotating grinding wheel that is guided along the component in straight, parallel lines.
Solarisation
The spiral arms of solarisation constitute a decorative finish applied principally to mainspring barrels and other larger round surfaces or wheels. The pattern is produced by rotating the part and the grinding wheel in opposite directions.
Perlage
Perlage is applied to the inside surfaces of plates and bridges as well as to the invisible dial side of the main plate. The cloudlike decoration is generated with a rotating abrasive peg that only briefly stipples the component. Perlage progresses from the outside to the inside of a part, and each stipple overlaps the previous one.
Straight graining
Straight graining is a finish applied especially to steel clicks, springs and yokes. This type of decoration is produced with abrasive paper across which the part is drawn in a longitudinal direction. The technique calls for straight but cautious movements to assure that the delicate linear pattern is applied to even the furthermost corners of the component.
Circular graining
Smaller wheels are finished with circular graining. The regular circular contours are produced when the part is rotated on abrasive paper.
Circumferential graining
This technique is used to embellish the vertical edges of the frame elements of a Lange movement. The finish is applied with a rotating abrasive peg. The part is manually pressed against the side of the abrasive peg.
Flat polishing
Up to two hours of precision work are needed to mirror-polish the surfaces of a whiplash spring, the endpiece of an escape wheel and other parts of the movement.
To flat-polish a component, the finisseur presses it into the pith of an elderberry shoot and guides it in figures of eight on films coated with progressively finer diamond powder. This process requires the utmost in concentration. Even a tiny grain of dust between the part and the polishing film, or excessive pressure on the part, can wipe out hours of work in a second.
Black polishing
Only very few and select parts are decorated with the intricate black polishing technique. This process can take several days. Using special abrasive pastes, the respective parts are manually polished on a tin plate until they appear to be black at a certain angle of incident light.
Chamfering
At A. Lange & Söhne, all of the edges of plates, bridges and levers are chamfered, a process that involves both bevelling and polishing. Lange’s finisseurs demonstrate their skills by producing chamfers with a consistently uniform width and angle on virtually every edge in a movement that is finished with this technique.
The bevels are also polished entirely by hand. Movement parts made of softer materials are prepolished with progressively smoother rubber tools and then finished with a polishing brush. Harder steel parts are polished with a rotating wooden wheel.
Polishing of internal angles
The degree of perfection of a timepiece comes to the fore in discreet but salient details. Connoisseurs look for them first: the internal angles of bridges and levers. If they are precisely defined and straight, they are unquestionably polished by hand, because only a human hand can execute the linear polishing motion needed to obtain such a result.
If the internal angle is rounded, it is justifiable to assume that it was machine-finished. Lange’s finisseurs use a pencil-like hard metal tool to polish internal angles. They cut and finish such angles entirely by hand.
Hand-engraved balance cocks
Every Lange watch has a hand-engraved balance cock or tourbillon cock. For several generations of watchmakers of the Lange family, the engravings of the balance cocks have been based on the same motif: it consists of flower petals that surround the central screw of the cock and a floral pattern that subtly follows the characteristic outlines of the component to which it is applied.
But at the same time, every engraving is unique. The depth of the cut and the curl of the lines are like an inimitable fingerprint – a personal signature that sets each individual timepiece apart from all others.
Explore further



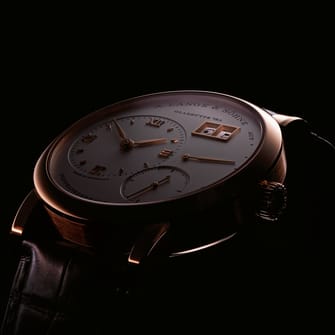
Exclusive insights into the world of fine watchmaking
Experience A. Lange & Söhne’s fascinating heritage, unique stories and exquisite timepieces by subscribing to our newsletter.
How can we be of service?
Whether you are in search of a specific model, have questions out of interest or need a service request for your timepiece – we are delighted to help you. We are at your service by phone, email or in one of our boutiques.
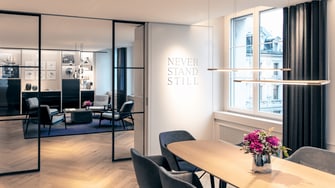