There are two sides to immaculacy. Obviously, it is forever unattainable. Then again, some people spare no effort to gradually approach it step by little step. That, in a nutshell, is the Lange way. The watchmakers in Saxony have but one goal: the perfect timepiece. All processes and procedures are aligned with the ambition to again push the limits of feasibility just a bit beyond where they seem to be. One of the consequences is that at A. Lange & Söhne, every movement is assembled twice. It makes no difference whether it is a simple three-hand calibre or a complication. And there are convincing reasons to do that.
One of them is related to a special design feature – the three-quarter plate introduced by Ferdinand A. Lange in 1864. On the one hand, it enhances precision by stabilising the entire wheel train beneath a single bridge. On the other, it makes assembly more difficult because even an experienced watchmaker has to mount and remove it several times in succession until each individual arbor has just the right endshake.
The other reason relates to the material of which the plate is made. At Lange, all plates and bridges are made of German silver. It is responsible for the rigidity of the movement and in the course of time develops a warm, golden patina that protects its surface. That is why the material is left „untreated“. Unfortunately, it has a disadvantage: a very sensitive surface. Every fingerprint can leave a lasting blemish and tools like screwdrivers may cause scratches.
This is why at A. Lange & Söhne many hours are invested in assembling each movement with utmost virtuosity. Afterwards, the interactions of all mechanical parts are adjusted to the highest degree of perfection. But then, the movement is taken apart again. Now, all parts are painstakingly cleaned, and many of them are lavishly decorated and polished. Even parts that later remain unseen are enhanced in this way. The jig screws used to assemble the raw movement are now replaced with new, thermally blued screws. When the three-quarter plate has been decorated with the characteristic Glashütte ribbing and the last gold chaton has been mirror polished, the movement is reassembled for the second and last time and carefully lubricated at over 50 oil sinks and bearing points with up to eight different greases and oils.
TWOFOLD ASSEMBLY AS PERFORMED ON THE RICHARD LANGE TOURBILLON „Pour le Mérite“
The assembly of a Lange calibre takes place in a long succession of meaningfully organised steps: First, the parts that have been lavishly finished by hand are clustered in so-called subassemblies that in turn are then merged to complete the entire movement. Here, the chain – it alone consists of more than 600 parts – is carefully wound around the spring barrel.
A small group of specially trained watchmakers devotes its undivided attention to a very special sub-assembly that requires a keen eye and the ultimate in dexterity: the tourbillon. It consists of 84 individual parts that together weigh no more than one-fourth of a gramme.
The assembly of the planetary gearing also requires extremely rare skills. After all, 38 tiny parts have to be accommodated in the fusée which has a diameter of only ten millimetres.
A special tool is used to fit the chain into the fusée’s grooves. Then, the finished movement is handed over to the reglage specialists who, as the engraving in the plate indicates, precisely adjust it in five positions.
The wheel train that indicates the time is now mounted on the dial side. The adjustment of the individual endshake tolerances requires considerable dexterity.
The pivoting dial segment mechanism is positioned and secured with screws. This procedure may need to be repeated several times to make sure all arbors have the right endshake. The mechanism assures that the subsidiary dial element is advanced by 90 degrees every six hours. Thus, it fully exposes the tourbillon from 12 to 6 o’clock and assures that the hour dial delivers a precise reading of the time from 6 to 12 o’clock.
Once the tourbillon cage has been integrated and attached to its bridge, the pivoting dial segment can be added. This completes the first assembly pass.
Now, the perfectly adjusted movement would be ready for integration in its case.
Instead, the movement is entirely taken apart again. The components are thoroughly cleaned in an ultrasonic bath. To assure the absolutely flawless presentation of the movement through the sapphire-crystal caseback, some parts are only now painstakingly decorated. The second assembly pass can begin.
In the second, final assembly phase, one single watchmaker is responsible for the entire movement. The three-quarter plate made of German silver was embellished with traditional Glashütte ribbing. All gold chatons have been manually polished and carefully inserted in the plate. The jig screws previously used were replaced with gleaming thermally blued screws.
The last step involves the placement of the pretensioning ratchet. The movement is finished and can now be cased up. Then, the watch must demonstrate its functional integrity and precision in an accurately defined procedure that can last several weeks.
RICHARD LANGE TOURBILLON “Pour le Mérite”
After the strict final inspection, the RICHARD LANGE TOURBILLON “Pour le Mérite” is ready for delivery. Somewhere in the world, a watch enthusiast is impatiently waiting for its arrival.
Explore further



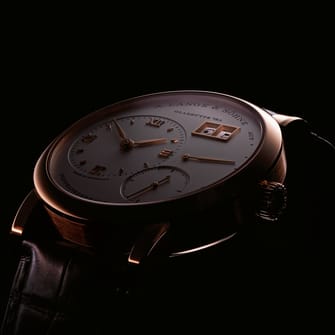
Exclusive insights into the world of fine watchmaking
Experience A. Lange & Söhne’s fascinating heritage, unique stories and exquisite timepieces by subscribing to our newsletter.
How can we be of service?
Whether you are in search of a specific model, have questions out of interest or need a service request for your timepiece – we are delighted to help you. We are at your service by phone, email or in one of our boutiques.
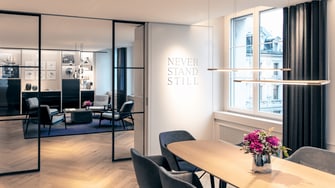