At A. Lange & Söhne, the ODYSSEUS is the cornerstone of a new watch family intended for active users. Its case has comparatively high water resistance and is protected against extraneous factors. The degree of artisanal immaculacy is particularly noteworthy in this timepiece segment. The parts are lavishly finished – even those that are concealed in the movement. Moreover, to assure superb quality, the movement is assembled twice.
Designing the ODYSSEUS
From the idea to the finished watch
The first conceptual deliberations concerning the ODYSSEUS model date back more than ten years. Work on the final version started four years ago. The Lange research and development team, consisting of developers, product designers, engineers, technicians and prototype makers, invested great passion and attention to details to convert a vision into a masterpiece. With each new model, they pursue the approach of developing a timepiece from the inside out, with the result that in the end, each new development is recognizable as a “genuine Lange”. The ODYSSEUS is thus also a typical Lange watch for a new activity profile
ASSEMBLING THE ODYSSEUS
TWO-FOLD MOVEMENT ASSEMBLY
Like all other Lange watches, the ODYSSEUS is assembled twice. Considerable dexterity is needed to perfectly fine-tune the interaction of all components. The complex initial assembly phase also includes the elaborate adjustment of the endshake of the small wheels of different sizes. In the process, the watchmaker must remove and refit the three-quarter plate several times to gradually optimise the endshake for every wheel. Once the movement has been assembled and tested, it is completely taken apart again. The parts are then cleaned. At this juncture, the three-quarter plate is endowed with Glashütte ribbing.
ASSEMBLY OF THE ROTOR
The rotor of the ODYSSEUS rotates in both directions and is unidirectionally winding. In its bearing, seven ceramic balls minimise friction. The outer centrifugal mass of the rotor is made of platinum and secured with five blued steel screws. The material of the central segment is black-rhodiumed Arcap. Arcap is an ideal material for a rotor because it is flexible and stable even if it is thin. This part is black-rhodiumed for aesthetic reasons. As far as the movement is concerned, the assembly of the rotor is the last step for the watchmaker. It requires great caution because the galvanised surface is extremely sensitive.
BEAT ADJUSTMENT
To ensure the accuracy and stable rate of the watch, it is important for the semi-oscillations of the balance to be symmetric. This is achieved with the precision beat adjustment system. The precise adjustment is performed with an eccentric and a whiplash spring. A screwdriver is used to move the eccentric on the hand-engraved bridge clockwise or anti-clockwise, thus changing the position of the index pointer. The whiplash spring on the opposite side keeps the pointer in the correct position.
CASING
The dial and the hands are fitted after the second assembly takes place and after comprehensive tests of the movement. Here, too, great caution is needed to prevent scratches. The polished hands are very sensitive, as is the brass dial. The movement is then integrated in the three-part case, after which the screwed caseback is secured. In the process, all seals are inspected and lubricated. Finally, the watch is tested for water resistance.
Finishing the ODYSSEUS
ARTISANAL FINISSAGE – DOWN TO THE SMALLEST DETAIL
Even though many parts of the movement are concealed, nearly every individual part is finished by hand. Various techniques are used in this process. Round parts such as wheels and the mainspring barrel are decorated with circular graining or solarisation. All frame parts are decorated with perlage. Perlage refers to the small overlapping cloud-like circles produced with a rotating abrasive peg. The contours of the frame parts are circumferentially brushed to achieve a matt surface that contrasts against the polished chamfers along the edges.
The three-quarter plate features Glashütte ribbing on the side, revealed by the sapphire-crystal caseback. The uniform stripes of the ribbing pattern are produced by a slightly inclined, rotating grinding wheel that is guided along the component in straight, parallel lines. The surfaces of springs and levers are often straight-grained to create a fine structure of parallel lines. This finish is obtained by rubbing the workpiece on abrasive paper in the longitudinal direction.
Engraving the ODYSSEUS
REFINED BY HAND
Created especially for the new model family, the wave pattern of the balance bridge is engraved by hand – and makes each ODYSSEUS unique. The individual engraving styles are like personal signatures. The dynamic of the waves and the depth of the cut as well as the tools themselves influence the final result. This is why our engravers personally craft and grind their burins to adjust the handle and the length of the steel point for the best fit. Even years later, an engraver can still tell whether he or a colleague worked on a particular movement part.
Explore further



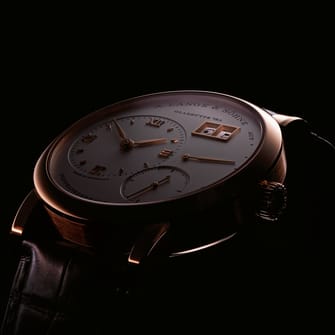
Exclusive insights into the world of fine watchmaking
Experience A. Lange & Söhne’s fascinating heritage, unique stories and exquisite timepieces by subscribing to our newsletter.
How can we be of service?
Whether you are in search of a specific model, have questions out of interest or need a service request for your timepiece – we are delighted to help you. We are at your service by phone, email or in one of our boutiques.
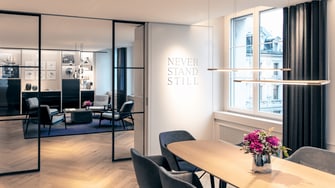